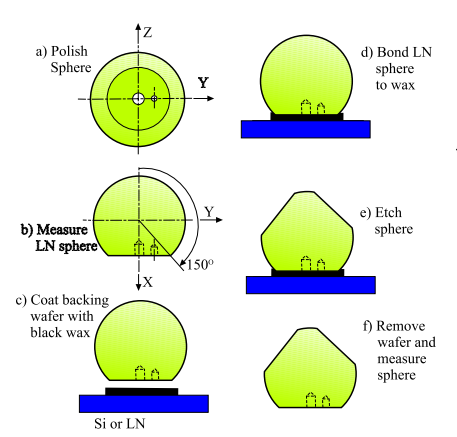
文章图片
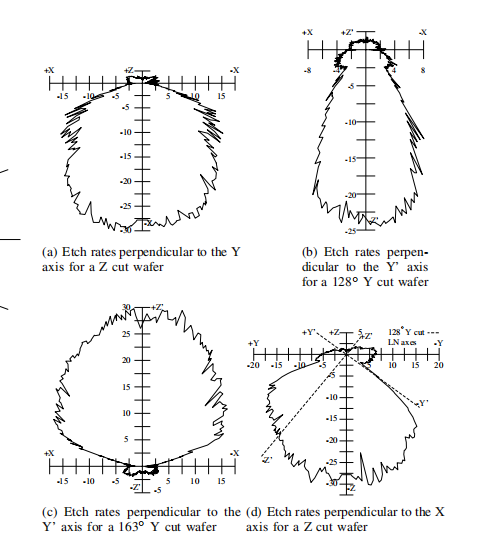
引言
铌酸锂是一种广泛应用于光学和声表面波器件的铁电材料 。 铌酸锂通常不用于微机电系统(MEMS)应用 , 部分原因是铌酸锂的体微加工不如与其他材料的加工那样好理解 。 已经公布了硅和石英对晶体取向的完全蚀刻率依赖性的数据 , 这允许模拟这些晶体的蚀刻 。 锗的类似数据也已发表 。 利用蚀刻模拟器 , 设计具有复杂结构的器件是可能的 。 我们做了铌酸锂腐蚀速率随晶体取向变化的实验 。 蚀刻表征是制造新传感器、致动器或其他新器件所需的基本技术 。 在这项研究中 , 在氢氟酸和氢氟酸与硝酸的溶液中蚀刻30毫米的铌酸锂球体 , 以确定蚀刻速率对晶体取向的依赖关系 。 发现最大蚀刻速率在-Z面上 , 并且蚀刻显示出关于Z轴的三重对称性 。
实验
用于蚀刻和测量LiNbO3球的过程与开发的过程相似 。 它们的过程和用于LiNbO3的过程之间的区别在于 , 一个掩模没有溅射在方向平面上 , 并且使用了一个更完整的球体 。 对于用Si进行的实验 , 由于蚀刻对称 , 只使用硅半球 。 LiNbO3与Si没有相似的蚀刻对称性 , 因此使用一个从0?到150?的可测量区域的球体来获得晶体更完整的蚀刻轮廓如图1(a , b) 。 此外 , 没有使用溅射掩模 , 以最小化由溅射导致的球体中的温度梯度 。 由于内部应力 , 球体中的温度梯度可能会导致球体断裂 。
图1 定向蚀刻速率依赖性实验的过程
实验过程如图1所示 。 为了在蚀刻过程中保护取向平坦 , 使用了黑蜡和支撑晶片 。 当蚀刻溶液是氢氟酸和硝酸时 , 硅背衬晶片被铌酸锂背衬晶片代替如图1(c) 。 否则 , 硅会发生自催化蚀刻 。 晶片支撑着蚀刻剂中的球体 , 并有助于保持黑蜡的完整性 。 蚀刻装置使用热水浴加热干燥烧杯中的蚀刻剂和球体 。 当球体和蚀刻剂达到实验规定的温度时 , 将球体放入蚀刻剂中 。
结果和讨论
图2(a)显示了蚀刻球体的示例 , 蚀刻速率分布示于图中 。 条件1和4分别为条件3和4 。 角度θ和φ的定义如图所示 。 在图2(b)中 , 3和4所示 , 圆的半径对应于图2中的φ 。 2(b) , 以及平面内的角度圆圈代表图2中的角度θ 。 从蚀刻图中可以看出 , 蚀刻呈现出关于Z轴的三重对称性 。
图2 蚀刻球体和角度定义
最大蚀刻速率在Z面 , 在两个蚀刻轮廓之间需要注意的另一个细节是 , HF蚀刻球体的蚀刻速率比HF:HNO3蚀刻球体的蚀刻速率更均匀 。
蚀刻模拟:
HF蚀刻球的数据被分成三个对称区域 。 这些区域被平均成一个对称区域 , 然后复制回其他区域以形成完整的数据范围 。 这有助于减少数据中的噪声量 , 并消除定向平面所在的空白区域 。 接下来 , 将平均数据旋转到使用晶体切割所需的正确方向 。 然后从球体中选择垂直于X、Y或Y轴的蚀刻速率数据并绘制 。 在图1中 , “Y”和“Z”指旋转的晶轴 , X、Y和Z指未旋转的晶轴 。 在图3(d)中 , 只给出了一个沿Y轴的图 , 因为铌酸锂的大多数晶体切割都偏离了Y轴 。 在图中 , 以128♀Y切割晶片的晶轴为例 。 通过旋转晶轴可以获得其他晶体切割的蚀刻速率 。 5(a)到5(c)为每个晶体切割选择一组单独的数据 。
图3 图为不同的晶体切割 。 所有的图表都显示了μm/h中的蚀刻率
将蚀刻的形状与预测的形状进行比较 , 模型预测的蚀刻形状与蚀刻晶片的轮廓非常一致 。 这表明蚀刻速率数据可以用于更先进的建模程序 。 晶面角度的测量值与使用预测值之间的差异源于晶轴对准的误差和蚀刻样品角度测量的误差 。 晶轴对准中的误差可以通过改善蚀刻球体的中心发现以及更好的对准标记来解决 。 误差小于4.3 ♀可以通过前面讨论的失调来解释 。
总结
【华林科纳半导体-----LiNbO3刻蚀速率与晶体取向的关系】我们对铌酸锂的刻蚀特性进行了初步研究 。 通过用氢氟酸和氢氟酸与硝酸的混合物蚀刻直径为30毫米的铌酸锂球体来收集数据 。 绘制蚀刻速率 , 给出整个球体的蚀刻速率 。 这些数据被用来预测蚀刻晶片的形状 。 预测的形状与蚀刻晶片的形状一致 。