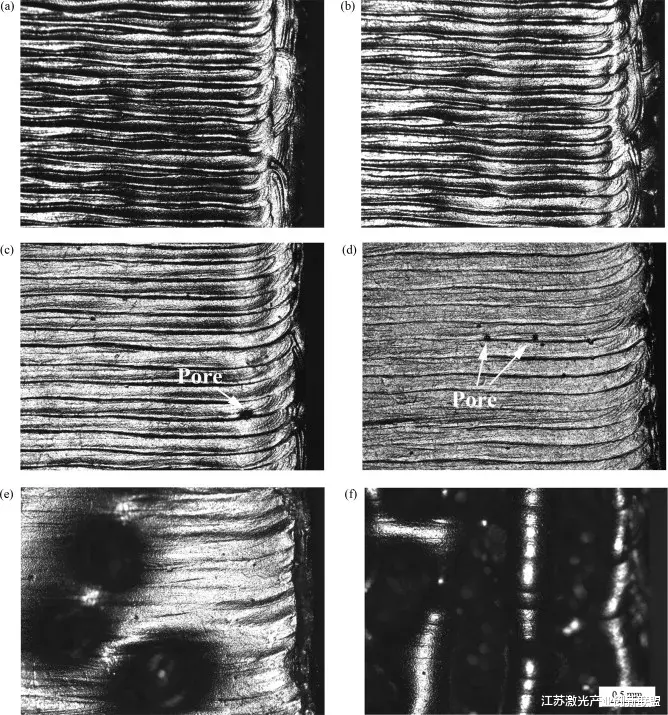
文章图片
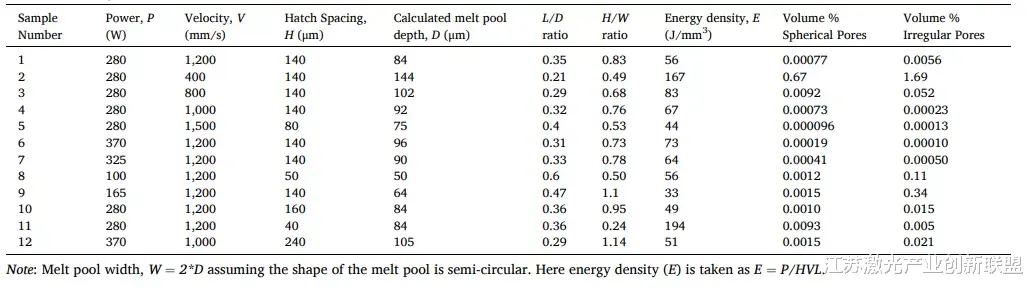
文章图片

文章图片

江苏激光联盟导读:
本文预测了LPBF材料中的大规模缺陷 , 探索了解决方法 。
摘要
准确的缺陷检测、表征和预测在全密度和无缺陷金属增材制造(AM)中具有巨大的潜在影响 。 因此 , 本文提出了缺陷结构过程图(DSPMs)作为一种量化孔隙率作用的手段 , 在粉末床印刷材料中作为一个示例缺陷结构 。 利用同步加速器微计算机断层扫描技术(μSXCT)研究了激光粉末床熔合(LPBF)材料的金属AM缺陷在加工参数空间内的可预测趋势 。 利用激光功率、扫描速度和舱口间距的变化 , 在EOS M290上制作了ti - 6al - 4v测试块 。 μSXCT在低激光功率、高扫描速度的过程空间区域发现了典型的欠熔或欠熔缺陷 。
这些缺陷与相邻熔体轨迹之间的不足重叠有关 , 可以通过应用熔体池几何建模的缺乏熔合准则来避免 。 大规模的钥匙孔缺陷也被成功地缓解了与浅钥匙孔前壁角相关的熔体池形态估计 。 与ti - 6al - 4v的标称(制造商推荐的)加工参数相比 , 工艺变量的选择导致深孔 , 即高激光功率和低扫描速度 , 球形孔隙率大幅增加 。 在完全致密的过程空间内也发现了缺陷 , 这与激光-粉末相互作用过程中气体孔隙转移到AM测试块有关 。 总之 , 这项工作表明 , 通过选择适当的工艺参数 , 可以成功地预测LPBF材料中的大规模缺陷 , 从而减轻/最小化缺陷 。
1.介绍
激光粉末床融合(LPBF)金属增材制造(AM)技术目前为零件生产提供了最好的再现性和尺寸精度 , 因此在工业界和学术界都得到了很好的研究 。 一般来说 , LPBF技术使用以下步骤来制造组件:(1)在机器内的构建板上铺上一层指定厚度的金属粉末;(2)用激光束选择性地熔化粉末层内所需的区域;(3)将构建板向下移动 , 在构建板上铺上一层新的粉末 。 这个过程一层一层地重复 , 直到零件制造完成 。 LPBF金属AM构建的积极工艺结果是由各种工艺参数控制的 , 包括但不限于束流功率(P)、扫描速度(V)、舱口间距(H)、层厚(D)和扫描模式等许多其他参数 。
EBM样本与聚焦偏移的顶部表面表征(所有图像都是相同的放大倍数) 。 (a) 4 mA. (b) 8 mA. (c) 12 mA. (d) 16mA. (e) 20 mA. (f) 24 mA.
EBM Ti-6Al-4V样品的表面拓扑如上图所示 。 与激光束相比 , 小的焦差值(4 mA)会导致光束斑集中 , 且在粉末层的穿透深度较大 。 以前的熔槽线部分熔化形成熔池 , 以确保熔槽的一致性和重叠 。 每条固化的舱口线形成一个山脊形状 , 造成粗糙的表面拓扑结构 。 但是 , 增大焦距偏移量会改变熔池的形态 。 焦点偏移显著提高了表面粗糙度 , 如图(c)和(d)所示 。 可以观察到细小的气孔 , 这可能是由于熔化的粉末释放出气态的氩气包裹在粉末颗粒中 。 然而 , 这些缺陷用阿基米德方法无法检测到 , 当下一层在z方向过熔后再熔前一层时 , 这些缺陷可能消失 。 当焦差增加到20 mA或24 mA时 , 肉眼可以看到大毛孔 。
大量研究表明 , 这些工艺参数的组合在很大程度上决定了熔体熔池的几何形状、局部组织、缺陷尺寸和缺陷形态 。 重要的是 , 不必要的LPBF缺陷 , 如孔隙度、夹杂物和氧化物 , 对金属AM组件的结构完整性和耐久性有害 , 特别是在航空航天和生物医学应用中 , 过早失效(如疲劳)主要由缺陷结构控制 。 Edwards和Ramulu发现 , 由于存在有害缺陷 , 无论表面条件或构建取向如何 , L-PBF Ti-6Al-4V的疲劳性能强度比变形合金低约77% 。 Masuo等确定 , 加工缺陷(包括表面粗糙度)将预制试样的疲劳强度限制在锻造ti - 6al - 4v疲劳强度的1/3左右 。 因此 , 将相关的工艺参数与产生的缺陷分布联系起来 , 以认证金属AM工艺和部件 , 尤其是结构材料和生物医学应用 , 过程-缺陷-性能关系是很重要的 。
SLM过程中激光熔化金属粉末的原理图 。
SLM中Zone III边缘参数和EBM中超线或焦点偏移导致的孔隙主要是熔体池重叠不足造成的 。 当激光或电子功率扫描粉末层时 , 粉末颗粒在瞬态过程中形成熔池 , 如上图所示 。 熔融材料与未熔粉的界面温度在熔点附近(Ti-6Al-4V为1660°C) 。
推荐阅读
- 国外男子被切除心脏后,仍活555天,得知原因,网友感慨:真伟大
- 未受精还天天下蛋,鸡怎么就沦为下蛋机器?鸡的BUG被人类利用了
- 宇宙的胎儿期,从大爆炸到决定世间万物,仅仅只用三分钟
- 元宇宙到底是啥?它对我们生活有什么利弊?
- 福建4名女子徒手偷走工地近百吨建材,平时工人搬运都需借助机器
- 暗能量:我们不断膨胀的宇宙中最大的谜团
- 世界上臭名昭著的三大发明:本该拯救人类,结果却成了杀人机器
- 在动物界,只有人类会得脚气吗?为什么?
- 19岁女孩怒砸金店柜台,上百万翡翠砸碎,120件翡翠全部遭殃